How to Pick the Most Suitable Chemical Defoamer for Your Unique Needs
How to Pick the Most Suitable Chemical Defoamer for Your Unique Needs
Blog Article
Comprehending Exactly How a Chemical Defoamer Works to Boost Industrial Processes
Chemical defoamers play a pivotal role in maximizing industrial processes by successfully alleviating foam-related challenges. Their ability to lower surface area tension and disrupt bubble development equates into smoother operations and boosted effectiveness. The systems behind their action and the selection of offered solutions require a closer assessment. Understanding these elements can disclose substantial insights into not only improving production yet also attaining price financial savings throughout several markets. What remains to be explored is just how these defoamers can be customized to satisfy particular functional demands.
What Is a Chemical Defoamer?
A chemical defoamer is a material especially created to lower or eliminate the development of foam in different commercial processes. Lathering can hinder production performance, influencing the quality and efficiency of items in industries such as food and drink, drugs, and wastewater treatment. Defoamers are important in these applications, as too much foam can bring about operational challenges, such as overflow, lowered mixing efficiency, and prevented heat transfer.
These representatives generally consist of a mix of surfactants, oils, and other additives that work to undercut the foam framework. They are made to swiftly move to the foam's surface area, efficiently damaging the surface area tension and enabling the collapse of bubbles. The choice of an ideal defoamer is necessary, as various formulations may be tailored for certain procedures or kinds of foam (Chemical Defoamer). Elements such as compatibility with other components, temperature level stability, and the designated application play a considerable function in the performance of a defoamer.
Systems of Defoaming Action
The mechanisms of defoaming action include intricate interactions in between the foam and the defoamer framework. When a defoamer is introduced to a lathering system, it moves rapidly to the surface of the foam bubbles, displacing the supporting agents that add to foam stability.
As smaller bubbles combine right into bigger ones, the total security of the foam lessens. In addition, particular defoamers might include hydrophobic elements that enhance their capability to destabilize the foam by developing a barrier that inhibits bubble formation. This twin action-- surface area tension decrease and destabilization-- permits an extra reliable malfunction of foam.
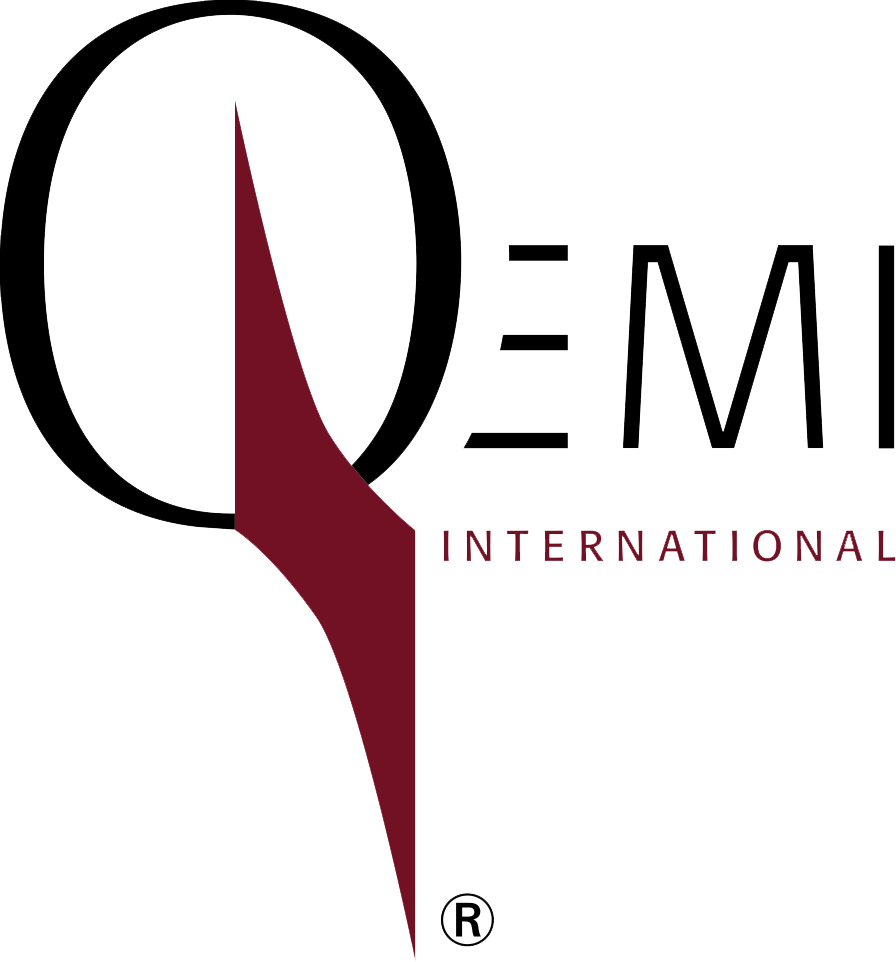
Moreover, the viscosity and dispersing characteristics of the defoamer play critical roles in its effectiveness. A well-formulated defoamer will certainly make certain quick migration and ideal performance, minimizing foam formation throughout industrial procedures. By understanding these devices, industries can better select and use chemical defoamers to improve functional performance and product high quality.
Types of Chemical Defoamers
Chemical defoamers can be categorized into several kinds, each tailored to particular applications and foam obstacles. The key categories include silicone-based, non-silicone-based, and powder defoamers.
Silicone-based defoamers are extremely reliable due to their capacity to spread rapidly throughout fluid surface areas. Non-silicone-based defoamers, on the other hand, typically depend on natural compounds like fatty acids or esters.
Powder defoamers are composed of strong bits that can be added to dry processes or solutions. They are usually utilized in procedures where liquid defoamers might not be reliable, providing an one-of-a-kind service for specific applications, such as in the production of specific types of plastics or powders.
Additionally, each type of defoamer can be tailored with numerous additives to enhance effectiveness, such as emulsifiers or surfactants, permitting adaptability in dealing with various lathering click site scenarios across several markets.
Applications in Industrial Processes

In the food and beverage industry, defoamers are important during the manufacturing of juices, beers, and dairy items, where extreme foam can impede blending and filtration procedures. By reducing foam development, defoamers help keep regular product quality and optimize processing times.
In drugs, the existence of foam throughout the blending and formulation of medications can affect dose accuracy and product stability. Defoamers guarantee smooth operations, therefore assisting in the manufacturing of high-grade drugs.
Wastewater therapy centers also count on defoamers to regulate foaming in aeration containers, which can otherwise decrease treatment performance and complicate sludge handling. By efficiently managing foam, these chemicals improve the total efficiency of therapy procedures and add to regulative conformity.

Advantages of Utilizing Defoamers
While foam can offer considerable challenges across various markets, making use of defoamers supplies many advantages that improve operational efficiency and product stability. Defoamers effectively lower or eliminate foam formation, resulting in smoother production processes and enhanced product quality. This reduction in foam minimizes disruptions during production, permitting continual procedure and increased throughput.
Furthermore, the application of great post to read defoamers can lead to cost financial savings by reducing the need for excess basic materials and energy usage associated with foam management. By maximizing the production process, manufacturers can attain higher returns and lower waste, inevitably improving profitability.
Furthermore, defoamers add to far better devices performance. Foam buildup can result in obstructing, overflow, and equipment wear, resulting in costly downtime and maintenance. By avoiding these problems, defoamers prolong the life-span of machinery and reduce functional prices.
Final Thought

A chemical defoamer is a material especially developed to decrease or remove the development of foam in numerous commercial procedures. When a defoamer is presented to a lathering system, it migrates rapidly to the surface of the foam bubbles, displacing the maintaining agents that add to foam security. A well-formulated defoamer will certainly ensure rapid movement and optimum efficiency, lessening foam development throughout industrial processes. Defoamers effectively minimize or remove foam development, leading to smoother production processes and boosted item quality.In final thought, chemical defoamers play an essential function in enhancing commercial procedures by efficiently reducing foam formation.
Report this page